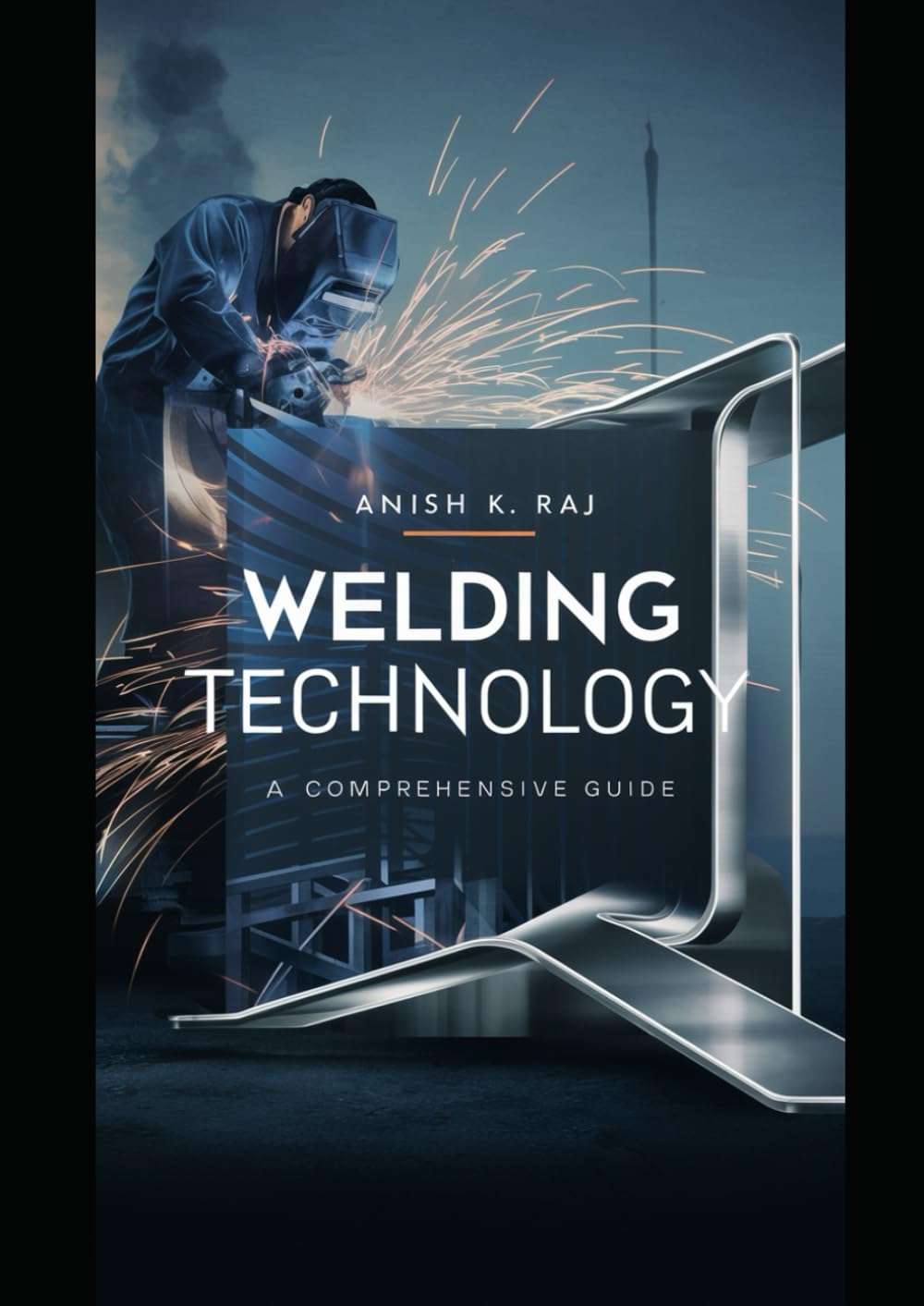
A Comprehensive Guide to Welding Technology
The world of welding is a fascinating blend of science, engineering, and artistry. From the intricate joins in skyscrapers to the robust welds in pipelines, welding technology underpins countless aspects of modern life. Understanding the various techniques, safety precautions, and career opportunities within this field is crucial for both aspiring welders and those seeking to appreciate the complexities of this essential industry. This comprehensive guide aims to illuminate the diverse facets of welding technology, providing a detailed exploration for those interested in learning more.
Understanding the Fundamentals of Welding
Before delving into the specifics of different welding processes, it’s essential to grasp the fundamental principles. Welding, at its core, is a fabrication process that joins materials, typically metals, by coalescing them at their melting points. This process often involves the application of heat, pressure, or both, to create a strong and durable bond. The strength and integrity of the weld depend heavily on various factors, including the type of metal being welded, the chosen welding process, and the skill of the welder.
Types of Welding Joints
Welding joints are categorized based on their geometric configuration, influencing the weld’s strength and suitability for specific applications. Common joint types include butt joints, lap joints, T-joints, corner joints, and edge joints. Each joint type requires a specific welding technique and preparation to ensure optimal results. The selection of the appropriate joint type depends largely on the design requirements and the materials involved.
Common Welding Processes
The welding world boasts a vast array of processes, each with its unique characteristics and applications. Some of the most widely used processes include:
- Shielded Metal Arc Welding (SMAW): Often referred to as stick welding, this process utilizes a consumable electrode coated with flux to protect the weld pool from atmospheric contamination.
- Gas Metal Arc Welding (GMAW): Also known as MIG welding, this semi-automatic process employs a continuously fed wire electrode and a shielding gas to protect the weld pool.
- Gas Tungsten Arc Welding (GTAW): Commonly called TIG welding, this process utilizes a non-consumable tungsten electrode and a shielding gas for precise and high-quality welds.
- Flux-Cored Arc Welding (FCAW): This process uses a tubular electrode filled with flux and a shielding gas, offering a combination of SMAW and GMAW characteristics.
Each of these processes presents unique advantages and disadvantages, making them suitable for different materials and applications. Factors such as weld penetration, speed, and cost-effectiveness need to be considered when choosing a welding process.
Safety in Welding: A Paramount Concern
Welding involves working with high temperatures, intense light, and potentially hazardous materials. Therefore, adhering to strict safety protocols is non-negotiable. Personal Protective Equipment (PPE) is crucial, including welding helmets with appropriate shade lenses, protective clothing, gloves, and respiratory protection. Proper ventilation is essential to mitigate the inhalation of harmful fumes and gases. Understanding the safety data sheets (SDS) for all materials used in the welding process is crucial. Regular safety training and adherence to established safety procedures are indispensable for a safe working environment;
Understanding Welding Hazards
Welding presents several potential hazards, including:
- Arc Eye: Exposure to intense ultraviolet (UV) and infrared (IR) radiation from the welding arc can cause painful and temporary eye damage.
- Burns: Contact with hot metal, sparks, or the welding arc can result in severe burns.
- Fume Inhalation: Inhaling welding fumes containing metallic oxides and other potentially harmful substances can lead to respiratory problems.
- Electrical Shock: Improper handling of welding equipment can lead to electrical shock.
- Fire Hazards: Welding sparks and hot metal can ignite flammable materials.
Awareness of these hazards and the implementation of appropriate safety measures are paramount in minimizing the risks associated with welding.
Welding Technology Advancements
The field of welding technology is constantly evolving, with ongoing advancements in equipment, processes, and materials. Robotics and automation are increasingly integrated into welding processes, leading to improved efficiency, precision, and consistency. New welding techniques and materials are continuously developed, enabling the joining of increasingly complex materials and structures. The development of advanced welding power sources and control systems further enhances the precision and control of the welding process.
Robotics and Automation in Welding
The integration of robots into welding processes has revolutionized the industry. Robotic welding systems offer significant advantages in terms of speed, accuracy, and repeatability, making them ideal for high-volume production applications. These systems can perform complex welds with exceptional precision, reducing the need for manual intervention and minimizing human error. Furthermore, robotic welding systems can operate in hazardous environments, improving worker safety.
New Materials and Processes
The development of new materials and welding processes is continually pushing the boundaries of what is possible. The ability to weld advanced materials, such as high-strength steels, aluminum alloys, and composites, has opened up new possibilities in various industries. Advanced welding processes, like laser welding and friction stir welding, offer superior weld quality and enhanced joint performance.
Career Paths in Welding
A career in welding offers a diverse range of opportunities, from working on construction sites to manufacturing plants and specialized industries. The demand for skilled welders remains high across various sectors, providing ample career prospects for those with the necessary skills and training. Career progression can involve specializing in specific welding processes, becoming a certified welding inspector, or even starting one’s own welding business.
Education and Training
Formal education and training are essential for a successful career in welding. Various vocational schools, community colleges, and trade schools offer comprehensive welding programs, providing students with the necessary skills and certifications. On-the-job training is also common, allowing individuals to learn from experienced welders and gain practical experience.
Specializations and Certifications
Within the welding field, various specializations exist, each requiring specific skills and certifications. Specializations may include structural welding, pipeline welding, or specialized welding of exotic materials. Certifications from reputable organizations demonstrate proficiency and adherence to industry standards, enhancing career prospects and credibility.